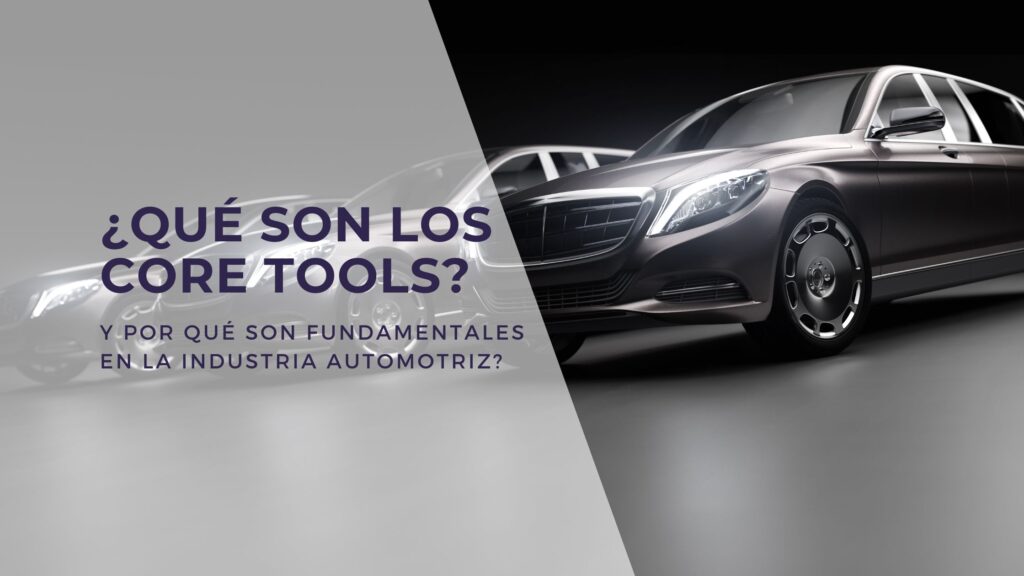
ISO 9004: el camino hacia la mejora continua más allá del cumplimiento
ISO 9004: El ca¿Qué son los Core Tools y por qué son fundamentales en la industria automotriz?
Introducción a los Core Tools
Los Core Tools, también conocidos como “Herramientas Clave de Calidad”, son un conjunto de metodologías y herramientas desarrolladas principalmente por la AIAG (Automotive Industry Action Group) para garantizar la calidad, confiabilidad y eficiencia en la producción de piezas y componentes dentro del sector automotriz. Estas herramientas se han convertido en el estándar de facto para los proveedores automotrices que desean mantenerse competitivos en un mercado donde la calidad y la mejora continua no son opcionales, sino una obligación.
Su importancia radica en que estas herramientas permiten un enfoque estructurado y preventivo en la gestión de calidad. En lugar de reaccionar ante los problemas una vez que han ocurrido, los Core Tools facilitan identificar riesgos potenciales, analizarlos, y poner en marcha acciones correctivas y preventivas antes de que se materialicen. Son esenciales para cumplir con los estrictos requisitos de los fabricantes de equipos originales (OEMs) como Ford, General Motors, BMW, Toyota, entre otros.
Origen y desarrollo de los Core Tools
El desarrollo de los Core Tools surge como una respuesta a la necesidad de estandarizar los procesos de calidad en la cadena de suministro automotriz. En los años 90, la AIAG, junto con grandes fabricantes como Chrysler, Ford y GM, colaboró para establecer métodos comunes que permitieran a los proveedores alinearse con los objetivos de calidad de la industria. Esta iniciativa fue clave para reducir la variabilidad en los procesos y asegurar una calidad constante en la producción.
Desde entonces, las herramientas han evolucionado con actualizaciones regulares, especialmente el FMEA, que fue renovado recientemente en colaboración entre AIAG y VDA (la asociación automotriz alemana), marcando una tendencia global hacia la armonización de estándares de calidad.
Objetivo de los Core Tools en la industria
El propósito principal de los Core Tools es proporcionar una base sólida para el desarrollo y manufactura de productos automotrices de alta calidad. Cada herramienta está diseñada para abordar diferentes etapas del ciclo de vida del producto, desde la planificación inicial hasta la producción en masa.
Entre los objetivos clave se encuentran:
- Detectar y prevenir defectos antes de que lleguen al cliente.
- Asegurar que los productos cumplan con las especificaciones del cliente.
- Establecer procesos robustos y controlados.
- Facilitar la mejora continua dentro de las operaciones de manufactura.
Estas herramientas no solo aplican a grandes ensambladoras, sino también a proveedores de primer, segundo y hasta tercer nivel que forman parte del ecosistema automotriz global.
Importancia de los Core Tools en la industria automotriz
En un entorno donde la competencia es feroz y los errores pueden representar pérdidas millonarias, los Core Tools se convierten en aliados indispensables para las empresas del sector. No solo ayudan a cumplir con normativas, sino que también fortalecen la reputación de la organización y mejoran la satisfacción del cliente.
Requisitos de calidad de la industria
La industria automotriz opera bajo estándares de calidad sumamente exigentes. Las fallas en productos como frenos, bolsas de aire o sistemas eléctricos pueden poner en riesgo vidas humanas. Por esta razón, tanto los OEMs como sus proveedores deben implementar sistemas de calidad sólidos que garanticen la trazabilidad, repetibilidad y confiabilidad de cada componente fabricado.
Los Core Tools permiten precisamente eso. Establecen una base técnica y metodológica que las organizaciones pueden seguir para diseñar, producir, verificar y mejorar productos y procesos.
Alineación con los estándares de la IATF 16949
La norma IATF 16949:2016 es el estándar global para los sistemas de gestión de calidad en la industria automotriz. Esta norma requiere explícitamente el uso de los Core Tools como parte del cumplimiento. Por ejemplo:
- El FMEA es una herramienta recomendada para la identificación de riesgos.
- El APQP es esencial para la planificación del desarrollo del producto.
- El PPAP se requiere para la aprobación de piezas antes de su producción.
El cumplimiento con IATF 16949 no solo es una ventaja competitiva, sino un requisito para hacer negocios con muchos OEMs. De ahí que las empresas que deseen certificarse bajo esta norma deban demostrar un dominio práctico de los Core Tools en todas sus operaciones.
Los cinco Core Tools esenciales
Los Core Tools se dividen en cinco herramientas principales, cada una con un propósito específico dentro del ciclo de vida del producto. Vamos a explorarlas una por una para entender su rol dentro del sistema de calidad automotriz.
APQP (Advanced Product Quality Planning)
El APQP, o Plan Avanzado de la Calidad del Producto, es uno de los pilares fundamentales dentro de los Core Tools. Su principal objetivo es asegurar que se cumplan todas las necesidades del cliente durante el desarrollo de un producto o proceso, desde su concepción hasta su producción en serie. Esta herramienta permite planificar y establecer pasos críticos que garantizan la calidad del producto desde el principio, evitando así errores costosos en etapas posteriores.
Etapas del APQP
El APQP consta de cinco fases principales que siguen un enfoque estructurado:
- Planificación y definición del programa: En esta etapa se identifican las necesidades del cliente y los requerimientos del producto. Aquí se realiza un análisis inicial de riesgos, estudios de factibilidad y la definición de los objetivos del proyecto.
- Diseño y desarrollo del producto: Se desarrolla el diseño del producto, sus especificaciones técnicas y los requerimientos del cliente. También se inician herramientas como el FMEA de diseño y el benchmarking.
- Diseño y desarrollo del proceso: Aquí se establecen las especificaciones del proceso de manufactura, incluyendo planes de control, instrucciones de trabajo y necesidades de maquinaria o equipo.
- Validación del producto y del proceso: Se fabrican piezas piloto y se realizan pruebas para verificar que el producto cumple con los requisitos. También se valida el proceso de producción.
- Retroalimentación, evaluación y acciones correctivas: Tras el lanzamiento, se recopilan datos reales del desempeño del producto y del proceso, y se implementan acciones de mejora continua.
Beneficios del APQP
Implementar el APQP de manera adecuada ofrece ventajas como:
- Reducción de cambios de diseño tardíos.
- Minimización de problemas en la producción.
- Mejora en la satisfacción del cliente.
- Establecimiento de un enfoque preventivo y no reactivo.
Esta herramienta impulsa la colaboración entre diferentes áreas (ingeniería, calidad, manufactura, compras) y asegura que todos los involucrados compartan los mismos objetivos de calidad.
FMEA (Failure Mode and Effects Analysis)
El FMEA es otra de las herramientas más poderosas dentro del conjunto de Core Tools. Se trata de un análisis estructurado que busca identificar posibles fallas en productos o procesos antes de que ocurran, evaluando su impacto y proponiendo acciones para eliminarlas o reducir su ocurrencia.
Tipos de FMEA
Existen principalmente tres tipos de FMEA:
- FMEA de diseño (DFMEA): Se utiliza durante el desarrollo del producto para evaluar las posibles fallas del diseño antes de que el producto llegue a producción.
- FMEA de proceso (PFMEA): Se enfoca en los procesos de manufactura, identificando posibles errores en la línea de producción que puedan afectar la calidad del producto.
- FMEA de sistema: Aunque menos común, analiza fallas potenciales a nivel de sistemas completos, muy utilizado en empresas que diseñan plataformas completas.
Cada tipo de FMEA se desarrolla en base a una tabla en la que se evalúa:
- El modo de falla.
- El efecto de esa falla.
- La causa potencial.
- La severidad, ocurrencia y detección (índices que permiten priorizar riesgos).
Impacto del FMEA en la prevención de fallos
El FMEA tiene un valor incalculable en la prevención de defectos críticos. Al anticipar riesgos y trabajar proactivamente en su mitigación, las empresas pueden evitar:
- Costosas devoluciones de productos.
- Pérdida de clientes.
- Daños a la reputación de la marca.
Además, el nuevo enfoque AIAG-VDA ha modernizado esta herramienta, introduciendo nuevas metodologías como el “Action Priority” (Prioridad de Acción) para mejorar la toma de decisiones.
MSA (Measurement System Analysis)
El MSA, o Análisis del Sistema de Medición, es esencial para asegurar que las mediciones utilizadas durante la fabricación y la verificación de productos sean confiables, precisas y consistentes. En pocas palabras, si no puedes medir correctamente, no puedes controlar ni mejorar un proceso.
Evaluación de sistemas de medición
El objetivo del MSA es estudiar la variación que introduce el sistema de medición en los datos. Evalúa la precisión, exactitud, linealidad, repetibilidad y reproducibilidad de los instrumentos de medición y del personal que los utiliza.
Este análisis es clave para responder preguntas como:
- ¿Podemos confiar en las mediciones que hacemos?
- ¿Qué tanto influye el operador en los resultados?
- ¿Qué margen de error tiene nuestro equipo de medición?
Si un sistema de medición tiene demasiada variación, los datos no serán confiables, lo cual afectará la toma de decisiones y puede llevar a aceptar productos defectuosos o rechazar productos buenos.
Tipos de estudios en MSA
Algunos estudios comunes dentro del MSA incluyen:
- GR&R (Gage Repeatability and Reproducibility): Evalúa si los instrumentos y operadores son consistentes en sus mediciones.
- Estudios de linealidad y sesgo: Determinan si el instrumento mide correctamente a lo largo de todo el rango.
- Análisis de estabilidad: Verifica si el sistema se mantiene estable a lo largo del tiempo.
Un buen sistema de medición permite diferenciar entre variabilidad real del proceso y errores de medición, lo que es crucial para mantener estándares de calidad en la industria automotriz.
SPC (Statistical Process Control)
El Control Estadístico del Proceso, conocido como SPC por sus siglas en inglés, es una herramienta que utiliza métodos estadísticos para monitorear y controlar procesos de producción. Su principal función es identificar variaciones en el proceso para tomar decisiones a tiempo y mantener la calidad dentro de los límites establecidos.
Uso de gráficas de control
Las gráficas de control son el corazón del SPC. Estas gráficas permiten observar cómo se comporta un proceso a lo largo del tiempo. Se utilizan para identificar dos tipos de variación:
- Variación común: Inherente al proceso, no requiere intervención.
- Variación especial: Señal de que algo fuera de lo común está ocurriendo, y debe investigarse.
Las más comunes son las gráficas X̄-R, P, y C, que permiten monitorear características continuas o por atributos dependiendo del tipo de proceso.
Control y mejora continua
El uso adecuado del SPC ayuda a:
- Detectar problemas antes de que afecten al cliente.
- Reducir desperdicios y retrabajos.
- Mejorar la eficiencia del proceso.
- Fomentar una cultura de mejora continua basada en datos reales.
El SPC también es fundamental para establecer “capacidad del proceso” y así demostrar si un proceso puede producir consistentemente dentro de las especificaciones.
PPAP (Production Part Approval Process)
El PPAP es el proceso que permite a un proveedor demostrar que comprende todos los requisitos del diseño del cliente y que su proceso de producción puede cumplir con esos requisitos de manera constante durante la producción real.
Elementos clave del PPAP
El PPAP incluye una serie de documentos críticos como:
- Plan de Control
- Estudios de capacidad del proceso
- Resultados de medición
- Evidencia de cumplimiento de requisitos
- Aprobaciones de diseño
- Muestra de piezas
Dependiendo del nivel de PPAP requerido (nivel 1 al 5), se deben presentar más o menos evidencias. El cliente revisa esta documentación antes de aprobar formalmente que el proveedor comience la producción en masa.
Relevancia en el lanzamiento de productos
Este proceso es clave para garantizar que las piezas producidas en masa son idénticas a las aprobadas en la etapa de desarrollo. Sin un PPAP aprobado, no se puede iniciar la producción para entrega al cliente. Además, permite detectar desviaciones a tiempo y minimizar el riesgo de errores durante el lanzamiento de nuevos productos
Cómo se relacionan entre sí los Core Tools
Una de las mayores fortalezas de los Core Tools es que no son herramientas aisladas, sino que se complementan y alimentan entre sí para formar un sistema de gestión de calidad robusto. Juntas, crean una sinergia que ayuda a prevenir fallas, optimizar procesos y mejorar la satisfacción del cliente.
Flujo secuencial de los Core Tools
El uso de los Core Tools sigue una secuencia lógica dentro del ciclo de vida del producto:
- APQP: Comienza con la planificación avanzada de calidad, estableciendo los requerimientos del cliente y desarrollando el producto y proceso desde cero.
- FMEA: Durante el diseño y desarrollo, se aplican análisis de modos de falla tanto al diseño (DFMEA) como al proceso (PFMEA).
- MSA: Antes de iniciar la producción, se verifica que los sistemas de medición sean confiables mediante estudios de repetibilidad y reproducibilidad.
- SPC: Con los datos reales del proceso en marcha, se monitorean las variables críticas mediante gráficos de control.
- PPAP: Una vez que todo está validado, se presenta al cliente la documentación que comprueba que el producto cumple con los requisitos.
Cada herramienta es un eslabón en la cadena de calidad. Por ejemplo, un FMEA puede derivar en la necesidad de un nuevo estudio MSA, o los resultados del SPC pueden retroalimentar el plan de control definido en el APQP.
Sinergia entre herramientas
Estas herramientas se potencian entre sí de múltiples maneras:
- El FMEA identifica modos de falla que deben ser controlados mediante SPC.
- Los elementos identificados como críticos en el FMEA requieren controles definidos en el plan de control del APQP.
- Para asegurar que las mediciones son confiables, se realiza un MSA de los dispositivos que controlan los parámetros del SPC.
- Todo esto se documenta y presenta al cliente en el PPAP.
Por tanto, cuando los Core Tools se utilizan de forma integrada, se logra una prevención de problemas mucho más eficaz. La calidad deja de ser responsabilidad de un solo departamento para convertirse en una cultura transversal dentro de la organización.
Ventajas de implementar Core Tools en la industria automotriz
Adoptar los Core Tools como práctica habitual dentro de las operaciones industriales conlleva numerosos beneficios que impactan directamente en la eficiencia, calidad y competitividad de una empresa del sector automotriz.
Mejora en la calidad del producto
Una de las principales ventajas es la mejora sustancial en la calidad de los productos entregados. Gracias al enfoque preventivo, es posible detectar errores antes de que lleguen al cliente. Esto se traduce en:
- Reducción de fallos y reclamos.
- Menor número de productos rechazados o reprocesados.
- Mayor satisfacción del cliente y reputación positiva de la marca.
La implementación sistemática del FMEA, el uso de SPC para el control de procesos y la validación con PPAP garantizan que el producto cumpla con las expectativas del cliente desde el primer lote.
Reducción de costos y desperdicios
La calidad no solo se traduce en satisfacción del cliente, sino también en ahorros significativos:
- Menos paradas en la producción por errores.
- Menor necesidad de retrabajos.
- Reducción en devoluciones y garantías.
- Disminución del uso innecesario de recursos (materiales, tiempo, mano de obra).
Además, al estandarizar procesos con APQP y validarlos con herramientas como MSA, se asegura una producción más eficiente y confiable.
También se reducen los riesgos legales o contractuales, ya que una correcta gestión de calidad documentada con PPAP y respaldada con estudios FMEA y SPC puede probar ante el cliente que la empresa cumplió con su parte del acuerdo.
Casos prácticos del uso de Core Tools
Para entender mejor el impacto de los Core Tools, es útil ver cómo se aplican en situaciones reales dentro de la industria automotriz.
Ejemplo de aplicación en una planta automotriz
Una planta de autopartes que produce sistemas de frenos comenzó a experimentar una alta tasa de rechazos por variaciones en el diámetro de los cilindros maestros. El equipo de calidad decidió aplicar los Core Tools de manera integrada:
- Se realizó un FMEA de proceso que identificó el torneado como etapa crítica y con alto riesgo de defectos.
- Se implementó un estudio MSA que reveló problemas de inconsistencia en los dispositivos de medición utilizados por los operarios.
- Se ajustaron los equipos de medición y se capacitó al personal.
- Se incorporaron gráficas de control SPC para monitorear las variables del torneado en tiempo real.
- Se actualizó el PPAP y se presentó al cliente la nueva validación del proceso.
En cuestión de semanas, la tasa de rechazo bajó en un 70%, se redujeron las devoluciones y la empresa fortaleció su relación con el cliente.
Resultados obtenidos con la implementación
Los resultados más destacados fueron:
- Mejora en la calidad percibida por el cliente.
- Reducción de costos por desperdicio y reprocesos.
- Mejora en la moral del equipo de producción al ver resultados positivos.
- Mayor capacidad de respuesta ante auditorías internas y de clientes.
Este tipo de casos demuestra que los Core Tools no son solo una obligación documental, sino una poderosa estrategia de mejora continua.
Desafíos comunes al aplicar los Core Tools
Aunque las ventajas son claras, muchas empresas enfrentan obstáculos al implementar los Core Tools de manera efectiva.
Falta de capacitación del personal
Uno de los mayores retos es la falta de formación técnica en el uso adecuado de estas herramientas. Muchas veces:
- Se implementan solo para “cumplir con la auditoría”.
- Se llenan los formatos sin un verdadero análisis.
- No se comprende el propósito de cada herramienta.
Sin una capacitación adecuada, los Core Tools pierden su eficacia y se convierten en una carga burocrática más.
Integración con sistemas ya existentes
Otra barrera común es la dificultad para integrar estas herramientas con otros sistemas de gestión existentes. En algunos casos:
- Las empresas ya usan software propios que no están alineados con los formatos de AIAG.
- Hay resistencia al cambio de parte de la alta dirección o del personal operativo.
- Falta apoyo tecnológico para automatizar parte del proceso.
Superar estos retos requiere compromiso organizacional, liderazgo claro y una visión estratégica sobre el valor de la calidad.
Mejores prácticas para una implementación exitosa
Para que los Core Tools sean verdaderamente efectivos, es crucial seguir una serie de buenas prácticas que permitan integrarlos en la cultura y operación diaria de la empresa. No basta con aplicarlos de forma superficial; se debe asegurar una implementación profunda, coherente y sostenible.
Capacitación continua
Una de las mejores inversiones que puede hacer una empresa es en la formación de su personal. Los Core Tools requieren conocimientos técnicos específicos, y su uso correcto marca una gran diferencia en los resultados.
Las mejores prácticas incluyen:
- Realizar entrenamientos periódicos para todos los niveles (operadores, ingenieros, supervisores, calidad).
- Certificar a los equipos en metodologías como FMEA AIAG-VDA, APQP 2ª edición, MSA, SPC y PPAP.
- Utilizar casos prácticos reales de la planta para reforzar el aprendizaje.
- Incluir evaluaciones post-capacitación para asegurar la comprensión del contenido.
Una fuerza laboral capacitada no solo mejora la calidad de los productos, sino que también incrementa la motivación del personal al sentirse más competente y valorado.
Cultura organizacional enfocada en calidad
Para que los Core Tools realmente funcionen, deben ser parte del ADN de la empresa. No basta con tener a un departamento de calidad aislado que “llene formatos”. La calidad debe ser responsabilidad de todos.
Algunos pasos clave para fomentar esta cultura son:
- Involucrar a la alta dirección en el impulso y seguimiento de los Core Tools.
- Establecer indicadores claros de calidad y compartirlos con toda la organización.
- Reconocer públicamente a los equipos que logran mejoras gracias a estas herramientas.
- Fomentar la retroalimentación continua entre áreas (producción, ingeniería, calidad, compras).
Cuando la cultura organizacional está alineada con la mejora continua, el uso de Core Tools se vuelve natural y sostenido en el tiempo.
El futuro de los Core Tools en la industria automotriz
El entorno industrial está evolucionando rápidamente, y con ello también deben adaptarse las herramientas de calidad. Los Core Tools no son ajenos a la transformación digital, y ya están comenzando a integrarse con nuevas tecnologías y metodologías.
Digitalización y automatización de procesos
Cada vez más empresas están migrando de formatos en papel o Excel a plataformas digitales especializadas que:
- Automatizan el llenado de formularios como el FMEA o el APQP.
- Integran análisis de SPC en tiempo real con sensores IoT.
- Facilitan la trazabilidad y el seguimiento de acciones correctivas.
- Centralizan la información en sistemas ERP o PLM (Product Lifecycle Management).
Esto no solo mejora la eficiencia, sino que también reduce errores humanos y facilita auditorías.
Core Tools y la industria 4.0
La industria 4.0 está revolucionando la manufactura con el uso de tecnologías como inteligencia artificial, machine learning, big data y realidad aumentada. Los Core Tools están comenzando a integrarse en este ecosistema.
Por ejemplo:
- SPC con IA puede predecir fallas antes de que ocurran mediante análisis predictivos.
- FMEA puede generar alertas automáticas cuando hay desviaciones en el proceso.
- PPAP puede integrarse con blockchain para garantizar la autenticidad de los datos de validación.
Esto convierte a los Core Tools en herramientas aún más poderosas, listas para los desafíos del futuro.
Conclusión
Los Core Tools son mucho más que simples requisitos documentales o herramientas de cumplimiento normativo. Son una estrategia sólida y comprobada para asegurar la calidad, prevenir errores, optimizar procesos y satisfacer a los clientes en un mercado tan exigente como el automotriz.
Cuando se aplican correctamente, estas herramientas permiten anticiparse a los problemas, controlar los procesos y garantizar que cada producto fabricado cumpla con los más altos estándares. Pero más allá de su aplicación técnica, los Core Tools requieren un compromiso organizacional real, una cultura de mejora continua y una visión de largo plazo.
Implementarlos no es tarea sencilla, pero los beneficios que aportan en términos de calidad, rentabilidad y reputación son incuestionables. En una industria en constante transformación, las empresas que dominen estas herramientas estarán mejor posicionadas para enfrentar los desafíos del futuro.
Preguntas Frecuentes (FAQs)
1. ¿Son obligatorios los Core Tools para todos los proveedores automotrices?
Sí, en muchos casos los OEMs exigen a sus proveedores el uso de Core Tools como parte del cumplimiento de la norma IATF 16949.
2. ¿Cuánto tiempo toma implementar correctamente los Core Tools?
Depende del tamaño de la empresa y su madurez en gestión de calidad, pero una implementación sólida puede tardar de 6 meses a 1 año.
3. ¿Puedo usar software para automatizar los Core Tools?
Sí, existen múltiples soluciones digitales que permiten digitalizar FMEAs, SPC, MSA y PPAP de forma más eficiente.
4. ¿Qué pasa si no utilizo los Core Tools y cometo errores de calidad?
Podrías enfrentar penalizaciones por parte del cliente, perder contratos o sufrir daños reputacionales graves.
5. ¿Cómo empiezo a capacitar a mi equipo en Core Tools?
Lo ideal es empezar con cursos introductorios y después profundizar con formaciones específicas para cada herramienta, ya sea con instructores certificados o plataformas e-learning.